在实际生产中,生产现场的情况千变万化,被控过程的要求多种多样,逻辑关系也比较复杂,对系统设计的要求较高。控制系统既要保证正常情况下对被控过程实施很好的控制,又要在突发严重情况下保护系统的安全。由于操作人员的生理反应不可能跟上生产变化速度,在突发事件、故障状态下难以确保生产安全。以往大多采用手动或连锁停车的方法使系统停运来实现对系统的保护。但停运后需要少则数小时,多则数十小时系统才能重新恢复生产,这对生产影响太大,造成的经济损失也比较严重。为了有效地防止生产事故的发生,减少开车、停车的次数,工程技术人员开发了一种既能保证对被控过程正常控制又能适应短期内生产异常对系统的保护的控制方案,即选择性控制。如图1为选择性控制系统框图。在图1中,主要是使用了一个信号选择器来对系统使用正常调节器还是取代调节器进行选择。显然,在任何时刻只会有一个调节器接入控制系统。
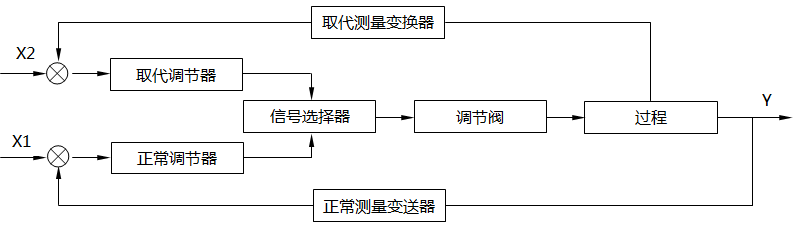
图1 信号选择器位于调节器的输出端的选择系统框图
选择性控制原理
选择性控制系统是把生产过程中的限制条件所构成的逻辑关系,叠加到正常的自动控制系统上去的一种组合控制方法。也就是系统中设有两个调节器(调节器或两个以上的变送器),通过(高、低值)信号选择器选出能适应生产安全状况的控制信号,实现对生产过程的自动控制。正常情况下当生产过程趋近于危险极限区,但还未进入危险区时,一个用于控制不安全情况的控制方案通过高值自动信号选择器、低值自动信号选择器将取代正常生产情况下工作的控制方案(正常调节器处于开环状态),用取代调节器代替正常调节器,直至使生产过程重新恢复正常。然后,又通过选择器使原来的控制方案重新恢复工作,用正常调节器代替取代调节器。因而这种选择性控制系统又被称为自动保护系统,或称为软保护系统。
从上述过程可见,设计选择性控制系统的关键环节是采用了信号选择器。信号选择器可以接在两个或多个调节器的输出端,对控制信号进行选择;或者接在几个变送器的输出端,对测量信号进行选择,以适应不同生产过程的需要。
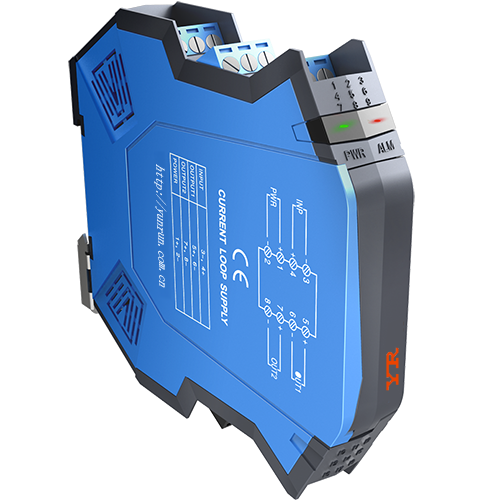
选择性控制系统分类
根据信号选择器在系统结构中的位置不同,选择性控制系统可分为两种:
①信号选择器位于调节器的输出端,对调节器输出信号进行选择的系统,如图1所示。这种选择性控制系统的主要特点是:两个调节器共用一个调节阀。在生产正常情况下,两个调节器的输出信号同时送至信号选择器,选出正常调节器输出的控制信号送给调节阀,实现对生产过程的自动控制。此时取代调节器处于开路状态,对系统不起控制作用。当生产不正常时,通过信号选择器选出取代调节器代替正常调节器对系统进行控制。此时,正常调节器处于开路状态,对系统不起控制作用。当系统的生产情况恢复正常,通过信号选择器的自动切换,仍由原正常调节器来控制生产的正常进行。这种选择性控制系统,在现代工业生产过程中得到了广泛应用。
②选择器位于调节器之前,对变送器输出信号进行选择的系统,如图2所示。该选择性系统的特点是几个变送器合用一个调节器。通常选择的目的有两个,其一是选出最高或最低测量值;其二是选出可靠测量值。如固定床反应器中,为了防止温度过高烧坏催化剂,在反应器的固定催化剂床层内的不同位置上,装设了几个温度检测点,各点温度检测信号通过高值信号选择器,选出其中最高的温度检测信号作为测量值,进行温度自动控制,从而保证了反应器催化剂层的安全。
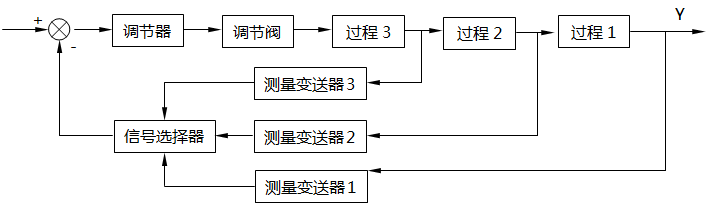
图2 信号选择器位于调节器之前的选择系统框图
推荐阅读
高值选择器和低值选择器八种典型应用