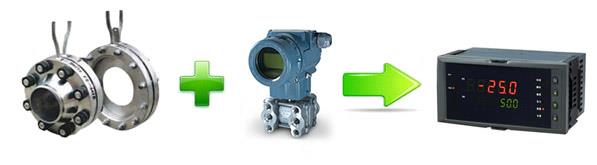

从式可看出:流出系数C,流束线胀系数ε,管道内径D,孔板开孔直径d,差压变送器测量的差压△P,被测流体的密度ρ等项,还有上式不包括的流量积算仪的误差,这些参数在使用现场如发生了变化,都将影响流量测量误差的大小。在现场是什么原因造成这些参数的变化呢?原因大致有:
A、如果孔板的几何形状,安装状态,管道及流体条件等不符合标准要求;孔板前后的直管段长度不能满足标准的要求;孔板圆心和管道圆心没有同轴;角接取压的取压孔位置不合要求;这些都会使流出系数C产生附加误差。
B、流束线胀系数ε,在设计孔板时是采用不变的ε值,但在现场如果流过孔板的被测介质压力发生变化,也会使流束线胀系数ε产生附加误差。
C、设计孔板时采用的管道内径D是指孔板前2D范围内的管道内径的平均值,在现场安装时,即使保证了孔板前10D、后5D是直线段,但工艺用的管道的尺寸是否合乎要求,如椭圆度、直度等,尤其是卷制管的管道内径D更难保证。
D、现场孔板安装的问题也不少,如孔板的安装大多是由管工和焊工来操作完成,有的管工和焊工根本就不听仪表工的指挥,使孔板的安装质量达不到要求是常见的事情。如法兰盘焊到管道后,法兰与环室配合处与管道轴心不同;法兰盘与管道内部接合处内部不打坡口,多数是不焊接不打磨,与安装图纸的要求差距很大。
E、再就是导压管的安装不注意要求,使正、负冷凝器或正、负取样管线不在同一水平面上,致使孔板产生的差压值难以正确传递到变送器去,而产生了附加误差。
F、使用条件和工作状态变化也是重要的影响因素。由于孔板是在特定条件下设计的,并且有一定的使用范围,如果使用条件、使用范围与标准不符,则设计、制造、安装得再标准也是不可能得到准确的测量结果的。当然温度、压力的变化是可以通过密度补偿的方法来减小测量误差的。还有就是饱和蒸汽的两相流向题,在问题“只有理解了蒸汽的特性,才能做好蒸汽流量的测量工作”有详细说明。
综合以上问题,可看出现场应用的情况多种多样,其所造成的流量测量附加误差是不能低估的,但要定量做出评估也是很困难的。要充分认识实验室的仪表精度与现场的应用精度是不能画等号的,即期望用精度高的差压式流量计在使用现场来得到精度高的测量结果是不可实现的。
相关阅读
流量积算仪流量系数K值计算与参数设置