这是一首流传广泛、影响很大的调节器PID参数调节口诀,该PID调节口诀最早出现在1973年11月出版的《化工自动化》一书中,流传至今已有几十年了。现在网上流传的PID调节口诀,大多是以该PID参数调节口诀作为蓝本进行了补充和改编而来的,如“曲线振荡频率快,先把微分降下来,动差大来波动慢。微分时间应加长”。还有的加了“理想曲线两个波,前高后低四比一,一看二调多分析,调节质量不会低”等。为便于理解和应用,现对该PID参数调节口诀进行较详细的分析。以下的分析及结论对临界比例度法、衰减曲线法也是有参考价值的。
先谈谈PID参数调节口诀“参数整定寻最佳,从大到小顺次查”中的“最佳”问题。很多仪表工都有这样的体会,在现场的调节器工程参数整定中,如果只按4:1衰减比进行整定,那么可以有很多对的比例度和积分时间同样能满足4:1的衰减比,但是这些对的数值并不是任意地组合,而是成对地,一定的比例度必须与一定的积分时间组成一对,才能满足衰减比的条件,改变其中之一,另一个也要随之改变。因为是成对出现的,所以才有调节器参数的“匹配”问题。而在实际应用中只有增加个附加条件,才能从多对数值中选出一对适合的值。这一对适合的值通常称为“最佳整定值”。“从大到小顺次查”中“查”的意思就是找到调节器参数的最佳匹配值。而“从大到小顺次査”"是说在具体操作时,先把比例度、积分时间放至最大位置,把微分时间调至零。因为需要的是衰减振荡的过渡过程,并避免出现其他的振荡过程,在整定初期,把比例度放至最大位置,目的是减小调节器的放大倍数。而积分放至最大位置,目的是先把积分作用取消。把微分时间调至零也是把微分作用取消了。“从大到小顺次查”就是从大到小改变比例度或积分时间刻度,实质是慢慢地增加比例作用或积分作用的放大倍数。也就是慢慢增加比例或积分作用的影响,避免系统出现大的振荡。最后再根据系统实际情况决定是否使用微分作用。
“先是比例后积分,最后再把微分加”是经验法的整定步骤。比例作用是最基本的控制作用,PID参数调节口诀说的“先是比例后积分”,目的是简化调节器的参数整定,即先把积分作用取消和弱化,待系统较稳定后再投运积分作用。尤其是新安装的控制系统,对系统特性不了解时,我们要做的就是先把积分作用取消,待调整好比例度,使控制系统大致稳定以后,再加入积分作用。对于比例控制系统,如果规定4:1的衰减过渡过程,则只有一个比例度能满足这一规定,而其他的任何比例度都不可能使过渡过程的衰减比为4:1。因此,对比例控制系统只要找到能满足4:1衰减比时的比例度就行了。
在调好比例控制的基础上再加入积分作用,但积分会降低过渡过程的衰减比,则系统的稳定程度也会降低。为了保持系统的稳定程度,可增大调节器的比例度,即减小调节器的放大倍数。这就是在整定中投入积分作用后,要把比例度增大10%-20%的原因。其实质就是个比例度和积分时间数值的匹配问题,在一定范围内比例度的减小,是可以用增加积分时间的方法来补偿的,但也要看到比例作用和积分作用是互为影响的,如果设置的比例度过大时,即便积分时间恰当,系统控制效果仍然会不佳。
在有的场合,也可不强求以上步骤,而是采取先按表1的PID参数凑试范围,把比例度、积分、微分时间选择好,然后由大到小的改变比例度进行凑试,直至调节过程曲线满意为止。积分时间和微分时间预置后用比例度凑试,其体现的是经验,如果没有经验就成为盲目调试了。此方法的缺点是当同时使用比例、积分、微分三作用时,不容易找到最合适的整定参数,由于反复凑试会费很多时间。
表1 经验整定法PID参数凑试范围一览表
控制系统 %(比例) Ti/min(积分) TD/min
温度 20-60 3-10 0.5-3
压力 10-70 0.4-3
流量 40-100 0.3-1
液位 20-80
“曲线振荡很频繁,比例度盘要放大”说的是比例度过小时,会产生周期较短的激烈振荡,如图1所示。且振荡衰减很慢,严重时至会成为发散振荡。这时就要调大比例度,使曲线平缓下来。
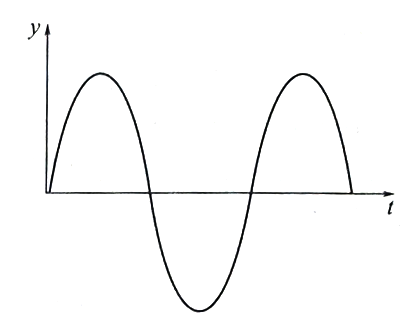
图1 比例度过小时的过渡过程曲线
“曲线漂浮绕大弯,比例度盘往小扳”说的是比例度过大时会使过渡时间过长,使被调参数变化缓慢,即记录曲线偏离给定值幅值较大,时间较长,这时曲线波动较大且变化无规则,形状像绕大弯式的变化,如图2所示。这时就要减小比例度,使余差尽量小。
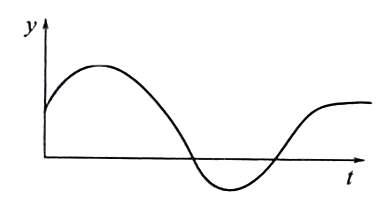
图2 比例度过大时的过渡过程曲线
“曲线偏离回复慢,积分时间往下降。曲线波动周期长,积分时间再加长”说的是积分作用的整定方法。当积分时间太长时,会使曲线非周期地慢慢地回复到给定值,即“曲线偏离回复慢”,如图3所示。则应减少积分时间。当积分时间太短时,会使曲线振荡周期较长,且衰减很慢,即“曲线波动周期长”,如图4所示。则应加长积分时间。
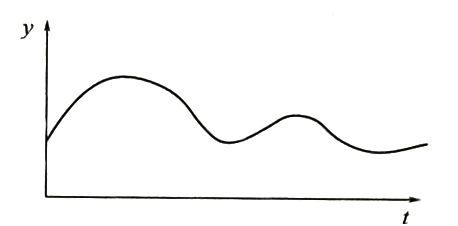
图3 积分时间太长时的过渡过程曲线
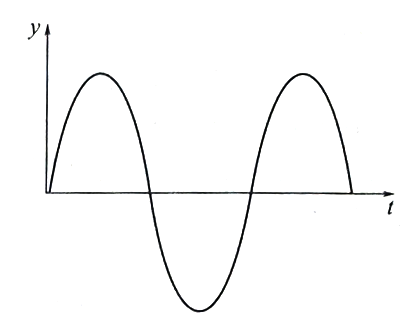
图4 积分时间太长时的过渡过程曲线
调节器的参数按比例积分作用整定好后,如果需启用微分作用时,则“最后再把微分加”。由于微分作用会增强系统的稳定性,故使用微分作用后,调节器的比例度可以在原来的基础上再增大一些,一般以增大20%为宜。微分作用主要用于滞后和惯性较大的场合,由于微分作用具有超前调节的功能,当系统有较大滞后或较大惯性的情况下,才应启用微分作用。
以上说的是孤立的调试方法,在实际调试中,由于比例、积分、微分作用的相互影响,所以要互相兼顾才能调试好。要掌握的是振荡过强则应加大比例度,加大积分时间;恢复过慢则应减小比例度,减小积分时间。加入微分作用后,要把比例度和积分时间在原有的基础上减小一些;通过调微分时间的凑试,使过渡时间最短,超调量最小。
为方便理解几十年前的PID参数调节口诀,云南昌晖仪表制造有限公司对PID参数调节口诀中的有关问题作点说明。
①什么是比例度盘?
由于历史的原因,当时仪表工接触的大多是气动调节仪表,20世纪70年代初电动仪表的应用也是有限的。气动仪表调整比例度就是改变一个针形阀门的开度,为便于观察阀门的开度,阀门手柄上有个等分刻度盘;电动仪表调整的是电位器,同样也有一个等分刻度盘;这就是口诀中说的“比例度盘”。
②过程曲线的观察
经验法的实质就是看曲线,调参数。现在使用的DCS功能强大,想观察什么曲线就可观察什么曲线,只要把测点引入DCS即可,非常方便。但以前由于条件所限,当时用得最多的是气动三针记录仪,还有电子电位差计记录仪。口诀中所说“过程曲线”大多指仪表的记录曲线,通常要设置较快的走纸速度和选择合适的量程,才有可能较好地观察到记录曲线。有的对象由于调节过程较快,从记录曲线读出衰减过渡过程是很困难的,只能凭经验观察,如调节器的风压或电流来回波动两次就达到稳定状态时,就可认为是n:1的衰减过渡过程。口诀中所说的过程曲线形状,是形象化、直观化、被放大了的曲线,其目的是为了便于理解。
③振荡周期和频率
过渡过程从一个波峰到第二个波峰之间的时间叫振荡周期,一个振荡周期是360°;振荡周期的倒数称为振荡频率。在衰减比相同的条件下,周期与过渡时间成正比,通常希望周期短一些为好,但各种被控对象的振荡周期相差是很大的,且周期的长短取决于所整定的对象,及不同的整定参数。口诀所说的“理想曲线两个波”,指的是在过渡时间内被调参数振荡的次数,如果说过渡过程振荡两次就能稳定下来,这就是很好的过渡过程。引入振荡周期和频率的概念是为了理论上分析问题的方便,与交流电的波形和频率相比,两者差别是很大的;过程控制的振荡周期是极缓慢的,大多长达数分钟至数十分钟,动次数而已。
④关于衰减比
在多数情况下,都希望得到衰减振荡的过渡过程,衡量衰减程度的指标是衰减比,即图5中B与B'两峰值的比,通常表示为n:1,一般n在4-10之间较妥。口诀中说4:1的衰减过渡过程好,是如何定出来的?这其实是工艺操作人员多年的经验总结。因为在生产现场投用自控系统的时候,被控工艺参数在受到干扰和调节器的校正后,能比较快地达到一个高峰值。然后又马上下降并较快地达到一个低峰值。如果工艺操作人员看到这样的曲线,心里就比较踏实,他知道被调工艺参数再振荡几次就会稳定下来了,是不会出现大的超调现象的。但是如果过渡过程是非振荡的过程,则工艺操作人员在较长的时间内只看到过程曲线在一直上升或下降,操作人员害怕出事故的心理,就会促使他调动相应地阀门改变工艺物料的大小以求指标稳定,由于人为的干扰会导致被调参数大大偏离给定值,这一恶性循环严重时,可能会使系统处于不可控制的状态,所以说选择衰减振荡的过渡过程,并规定衰减比在4-10:1之间,是根据工艺操作人员的实践经验得来的。
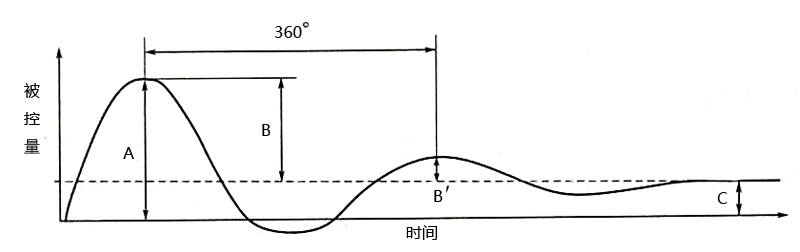
图5 过渡过程质量指标示意图
⑤最大偏差与超调量
最大偏差表示控制系统偏离给定值的程度,也就是当干扰产生,经过调节待系统稳定后,被调量与给定值的最大偏差。对于衰减振荡的过渡过程,最大偏差就是第一个波的峰值,即图5中的A。一个整定好的调节系统,一般第一个波波动最大,经一大一小两个波后,也就无所谓最大偏差了。
有时也用超调量来表示被控参数的偏离程度,超调量是衡量被控参数在过渡过程中振荡超出最终静态值的程度,即图5中的B。在实际应用中,超调量大多是用余差的百分数来表示,即图5中的B/C×100%。
推荐大家阅读黄文鑫编著的新书:《教你成为一流仪表维修工》、《仪表工问答》,对仪表工提高仪表维修维护能力很有帮助。本站可免费下载,下载地址 //ny-tec.com/servicecentre/list_126.html
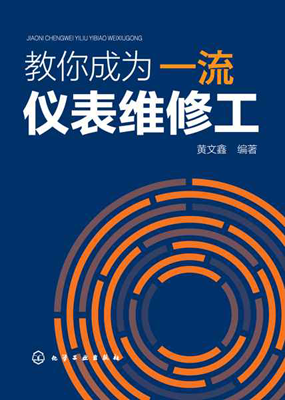