本文将考察当前流程工业现场设备、数据内容、传输要求等。在此基础上,本文提出流程工业现场数据传输网构想,为建设新一代流程工业现场数据传输高速公路提供选项。
第1类设备:模拟类仪表和模拟数字混合仪表
模拟数据是指用连续变化的物理量所表达的信息,如温度、湿度、压力、长度、电流、电压等等。模拟信号在一定的时间范围内可以有无限多个不同的取值。
在数字电路发明之前,生产流程状态参量都是以模拟信号形式传送的。生产流程参量在现场仪表中转换为电压或者电流模拟信号,通过电缆送到控制系统。当前模拟信号基本上以4-20mA和开关量为主。4-20mA电流信号在1970年代就被IEC确定为标准,至今仍然是现场仪表信号传输的主流方式。
第1类设备的模拟数据(下称1a类数据)用于生产控制,对数据传输的要求是高可靠性和确定性时延。可靠性是指数据要可靠地从现场仪表传输都位于控制室的控制器以及上位机,一般采取冗余设备和数据传输路径来保证。确定性时延是指现场数据要在确定的时间内传输到控制器,或者相反。根据工艺控制对象不同,这个要求一般在1ms到1000ms之间不等。
一个典型的大型石化综合装置,1a类数据数量大约在10万~20万之间。中小型石化和化工装置,1a类数据数量大约在1千~10万之间。
第1类设备的数据包括叠加在模拟信号之上的管理配置数字类数据(下称1b类数据)。这一类数据以HART协议数据为当前主流。
HART协议是美国ROSEMOUNT公司(现属于EMERSON)于1985年推出的一种用于现场智能仪表和控制室设备之间的通信协议。HART协议提供低带宽和适度响应时间的通信,目前在流程工业现场信号传输上得到广泛应用。
HART协议采用基于Bell202标准的FSK频移键控信号,在低频的4-20mA模拟信号上叠加幅度为0.5mA的音频数字信号进行双向数字通讯,数据传输率为1.2kbps。由于FSK信号的平均值为0,不影响传送给控制系统模拟信号的大小,保证了与现有模拟系统的兼容性。
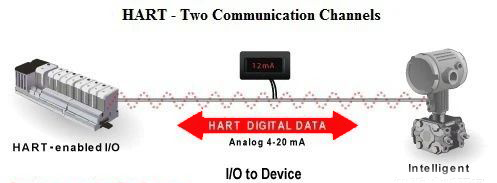
1b类数据主要用于仪表的配置和管理。这类数据对传输的可靠性和时间确定性要求比1a类数据低。事实上,HART数据以其传输速度低闻名,但是由于HART技术实现了初步的数字化,这个缺点没有阻碍其得到广泛应用。
1b类数据内容要比1a类数据丰富很多。在一台第1类设备中,1a类数据一般仅是一个浮点数,1b类数据可能有上百个不同类型的数据。
第2类设备:现场总线仪表
现场总线技术是一种应用于工业自动化领域的通信技术,它允许在生产现场的智能仪表和自动化控制系统之间进行数字信号的双向传输。这种技术通过使用总线架构,使得多个设备能够共享同一通信介质,从而实现信息的交换和控制任务的协调。现场总线技术具有节省线缆、简化系统设计、安装和维护等优点。
不同的厂商开发了许多类型的现场总线技术,仅IEC61158规定了20种现场总线标准。在流程工业,应用较多的有FF总线技术和PROFIBUS DP/PA技术。
现场总线传输内容包括1a类流程参量和1b类管理配置数据,其数据传输要求也与上述要求相同。与第1类设备不同的是,现场总线设备将这两类数据都通过数字形式在总线上传输,能够传输更多的流程参数和管理配置类数据。
由于产品设计和应用等原因,现场总线技术一直没有得到市场普遍接受。一般认为,流程工业中现场总线仪表占总仪表数量的10%~15%之间。
第3类设备:RS485类仪表
由于RS485具有更高的带宽,可以传输更多的数据。基于RS-485的MODBUS RTU协议简单易用,标准公开,逐渐成为现场复杂仪表的数据传输协议。
比较典型的RS485仪表有电动执行机构、储罐计量仪表、装车批量控制器、现场PLC控制器等。
有些仪表支持第1类模拟数据传输,但是也保留了RS485接口,用于管理和配置类数据通信。
支持RS485技术的仪表约占现场仪表设备的15%~20%之间。
RS485/MODBUS RTU的缺点是组网困难、数据无语义等。这导致了RS-485只能用于近距离小型网络或者诊断数据接口。
第4类设备:工业以太网设备
工业以太网是基于以太网技术的一种专用网络,用于工业自动化和控制系统中的数据通信和传输。与传统以太网相比,工业以太网具有更高的可靠性、实时性和安全性。它通过标准化的通信协议和硬件接口,实现设备之间的互联和信息交换。
目前在流程工业现场应用较为广泛的工业以太网协议有下面几种:
1、MODBUS TCP
MODBUS TCP是一种基于TCP/IP协议的通信协议,它是MODBUS协议的扩展,允许通过以太网进行数据交换。MODBUS TCP通过将MODBUS映射到TCP/IP协议上,使得它能够适应标准TCP/IP网络环境,实现更广泛的应用。
2、Ethernet/IP
Ethernet/IP由ODVA(Open DeviceNet Vendors Association)开发,用于连接工业自动化设备。它基于以太网技术,并结合了CIP(Common Industrial Protocol)通信协议,旨在提供一种高效、可扩展和安全的网络通信解决方案。
Ethernet/IP广泛应用于制造业、过程控制、能源管理和其他工业自动化领域,它结合了以太网的普及性和CIP协议的强大功能,为工业自动化提供了一个高效、可靠的通信平台。
3、PROFINET
PROFINET是由德国西门子公司主导,与PROFIBUS和PNO(PROFInet组织)合作开发的工业以太网标准。它是一个开放的以太网通信协议,专为工业自动化和过程控制领域设计,旨在实现设备和系统之间的高效、可靠和实时的数据交换。PROFINET为工业自动化和过程控制提供了一个高效、可靠和安全的通信平台,有助于提高生产效率和灵活性。
工业以太网设备网络接口符合IEEE802.3系列标准,一般采用RJ45或者光纤接口。这也限制了工业以太网协议在现场仪表上的应用。一般只有大型现场设备支持工业以太网接口,如大型色谱分析仪、PLC控制器、人机界面、工控计算机、变频器等。
以上4类设备是当前流程工业主流现场仪表设备。
根据SPE/APL技术特性,考虑构建流程工业现场数据传输网。网络架构如下图所示。
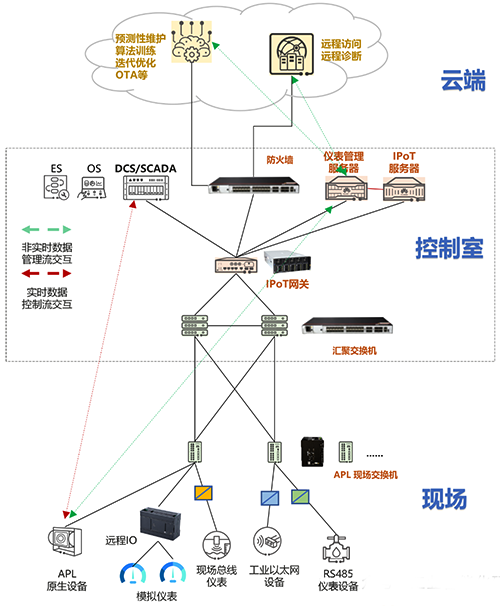
SPE/APL现场交换机支持下行SPE接口。现场部署的SPE/APL仪表通过双绞线接入现场交换机。传统仪表通过远程IO或者转换器接入现场交换机;若干台现场交换机与汇聚层交换机组成星形或者环形网。控制室内部署的控制器、上位机通过汇聚层交换机和IPoT网关接入控制网。网络通过防火墙接入云端服务器。
本文篇幅有限,仅讨论接入接入设备到APL现场交换机的数据传输。
第1类设备:模拟类仪表和模拟数字混合仪表
本类设备控制数据以模拟电流电压或者开关量形式传输,管理配置数据以HART形式传输。数据传输量小。可以考虑采用远程IO,在现场将模拟信号转换为数字信号,与HART数据汇总后通过APL分支通路上行接入APL现场交换机。
第2类设备:现场总线仪表
现场总线仪表已经实现了传输信号的数字化,只是数据传输格式与SPE/APL的以太网信号不同。第一种解决方式是APL交换机在接入侧将现场总线信号转换为以太网信号。P+F开发的一款APL现场交换机就支持PROFIBUS PA仪表的接入;第二种方式现场总线/APL转换器将现场总线信号转换为以太网信号,接入APL现场交换机。
第3类设备:RS-485类仪表
有两种形式。第一种输出模拟信号,同时支持RS485接口。第二种仪表只支持RS485接口。第3类仪表一般采用MODBUS RTU协议。使用RS-485/APL转换器,将MODBUS RTU数据转换为MODBUS TCP协议数据。设备接入APL现场交换机。
下图是储罐计量仪表系统图。储罐仪表输出RS485信号,组网后接入自动巡检仪,转换为标准以太网信号后,接入上位机。
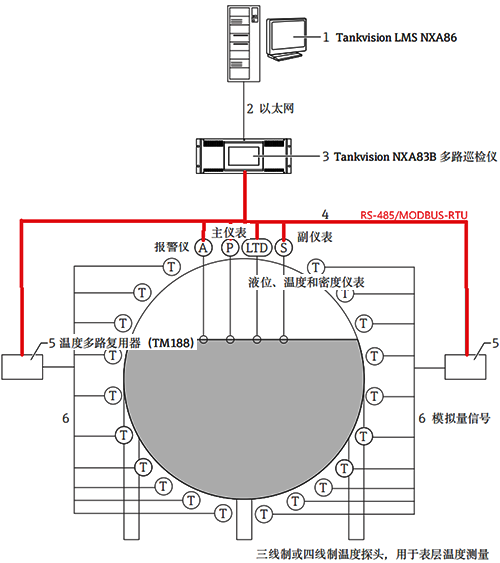
采用新型现场数据传输网改造上述系统。使用RS485/APL转换器,将RS485数据转换为APL以太网数据。储罐计量数据通过现场数据传输网接入自动巡检仪和上位机。
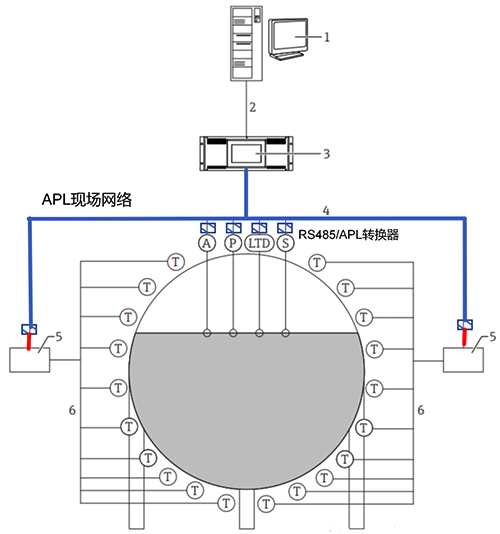
新方案的优点有:
1、现场数据传输网速度比RS485总线高;
2、现场数据传输网可以配置成冗余路径,数据传输可靠性更高;
3、现场数据传输网是公用现场数据传输基础设施,而非RS485专用总线,网络配置灵活性提高,数据传输成本降低。
第4类设备:工业以太网设备
第4类设备已经是工业以太网设备,只需将网线和RJ45接口转换为APL单对线介质即可。其余与第3类设备相同。
第0类设备:原生APL接口设备
以上讨论了存量设备接入现场数据传输网的方式。事实上,随着技术发展,越来越多的设备将支持APL接口,不需要各种转换器,可以直接接入现场数据传输网。某大型仪表制造商的大部分现场仪表已经支持PROFINET/APL数据接口。APL设备直接入网将是未来工业数据传输的主要方式。
现场数据传输网将在流程工业现场构建工业数据传输高速公路。当前存量仪表设备和未来的原生SPE/APL智能设备的数据能够高速传输。这些数据将有助于流程工业高效安全稳定生产,创造更高价值。