基于系统动力学分析了问题。我模拟了炼油厂的燃料消耗与裂解气产量随时间的变化。根据我的计算机系统动态分析,关键问题是延迟焦化装置裂解气的循环生产。我给炼油厂总经理的报告的结论是:
①液化石油气蒸发器对延迟焦化装置裂解气产量的变化反应太慢。
②焦化器和蒸发器的系统时间常数不同步。
③必须开发一种基于实时动态的前馈式先进计算机控制,以使焦化蒸发器系统达到动态实时平衡。
④应该聘请一组外部顾问,即这项技术的专家来提供这项计算机技术。
六个月过去了。如图1所示,复杂的前馈计算机系统被集成到液化石油气补给和燃料控制中。
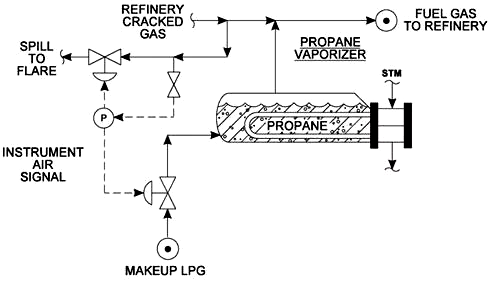
图1‑3由液化石油气补给控制阀故障引起的无意燃烧是分程压力控制的一个例子
炼油厂的火炬一如既往地继续着。现在怎么办?
心疼,气馁,沮丧,我出去看蒸发器。我看了蒸发器好几个小时。过了一会儿,我注意到燃料气体系统的压力在下降。这每3小时发生一次,是由延迟焦化装置的周期操作引起的。这很正常。
燃气压力下降导致液化石油气补给阀的仪表空气信号增加。这是一个“气开”阀,需要更多的空气压力来打开丙烷流量控制阀。这很正常。
但是,阀门位置本身没有移动。阀门卡在关闭位置。这不正常。当燃料气体压力下降时,控制室的操作员看到液化石油气丙烷补给阀打开。但是面板操作员并没有真正看到阀门的位置;他只看到阀门的仪表空气信号。
突然,阀门猛地打开了。丙烷呼啸着穿过阀门。汽化器中的局部液位指示飙升,燃料气体压力也是如此。火炬阀门打开以释放多余的工厂燃料气体压力,并保持打开,直到蒸发器液位下降,这需要一个多小时。这一切都让我想起了我在新奥尔良的车库那扇黏糊糊的侧门。
我用WD-40喷控制阀杆,用气压上下开关阀门十几下,清洗阀杆直到闪闪发光。下一次延迟焦化器循环时,液化石油气的流量缓慢增加,以捕捉下降的燃料气体压力,但不会超过压力设定值并开始调节。
我的错误是我认为现场仪表和控制阀工作正常。我没有考虑控制阀故障的可能性。但至少我从我的错误中吸取了教训。
找到问题比解决问题更难,工业现场有的决策不能解决问题往往是没有找到问题的根本原因。多问几个为什么,谨慎决策说着容易,做起来并不容易。
这个故事也告诉我们,如果不能有的放矢,盲目认为新控制算法或者新优化方法能解决现场的问题往往事与愿违。